Manufacturing
Our Resilient Manufacturing Process
When operating at capacity the plant will use more than 60 million pounds of raw materials to make coatings. When mixed into a paste this will fill up the Eagles stadium to a height of ten feet.
When operating at capacity the plant can make 50 million square yards a year when running 3 shifts a day for 5 days. This is 7,000 miles a year, enough to cover the highway between Philadelphia and Los Angeles in both directions.
The Congoleum sheet plant is the only 16 foot wide sheet vinyl manufacturing plant in North America.
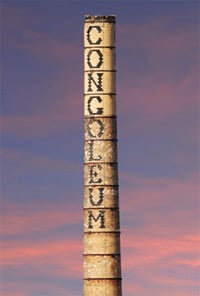
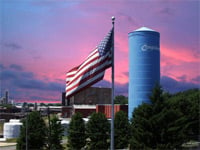
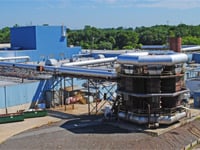
Raw Materials
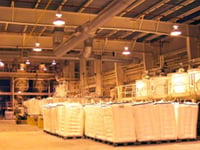
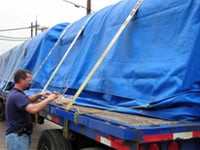
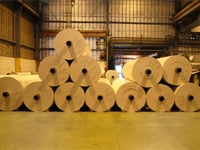
Rolls of felt from the Congoleum plant in Finksburg, MD are delivered to the plant. Felt rolls vary in thickness and width depending on the product it is meant for. PVC resin is received in 2000 pound bags from Europe, South America and Japan. These bags are unloaded into 200,000 pound silos for storage. Crushed limestone rock is delivered and also unloaded into different silos. Liquids are delivered on tankers and unloaded into 100,000 pound tanks for storage.
Mixing of Coatings
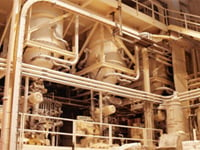
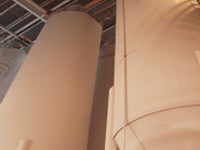

Once the powders and liquids have been stored in the large silos and tanks, they need to be mixed into a paste which makes the basic coating for all Congoleum resilient sheet products. The operator keys in the recipe and the system mixes the coatings. The computer is able to call for specific weights of the raw materials so that the automated system ensures that every batch of coating is the same as the previous batch. This equipment was installed in 2000 at a cost of $15 million USD.
Applying the Foam Layer
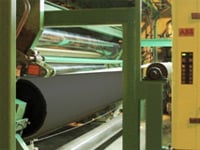
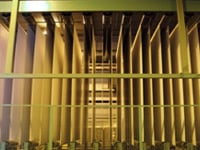
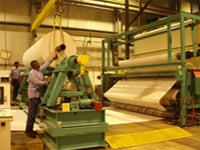
Vinyl resins, fillers and liquid plasticizers are mixed into a thin paste that is spread onto the felt carrier. The thickness of this `gel` layer can change depending on the quality characteristics specified for the final product. On line inspection is performed for visual defects and physical properties. Felt carrier rolls are fed into this line, the rolls are unwound into an accumulator that allows for delay in the process to tolerate roll changes. The coater applies the gel to the accurate thickness. Then the gel is cured in a large oven, the fumes are destroyed before being released and the finished product is wound and ready for printing.
Making of the Print Ink
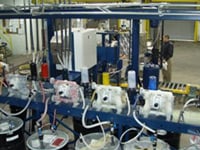
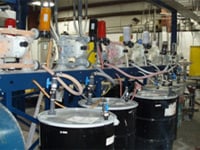
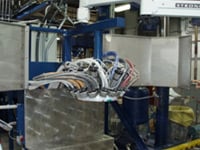
Latex, colored pigments, inhibitors and additives are delivered to the ink making room. Each ink has a color standard that must be matched. The ink system scans a color and breaks down the ink color into the pigments and recycled ink necessary. The system is programmed to use as much recycled ink as possible. Once completed a color check is done and once accepted, the completed drums of ink are sent to the print line where they are loaded into the press.
The Print Line
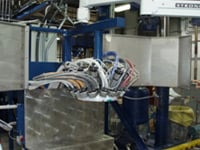
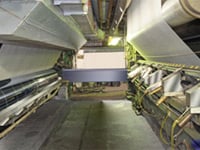
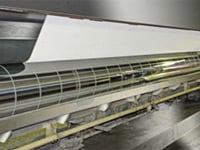
The decorative image is created by rotogravure printing. Up to 6 print cylinders rotate in a different color ink and transfer the cylinder image to the moving sheet. Each part of the printed image is dried before the next part of the image is applied onto the smooth white gelled sheet.
All 6 print cylinders must be printed exactly in line with the previous cylinder or the image will look fuzzy. Computer control systems take care of this. For every design change, the print cylinders must be changed. For every color in a design the inks must be changed.
Before printing begins each shade of ink is inspected to ensure the color is perfectly aligned with what the design calls for.
The Wearlayer
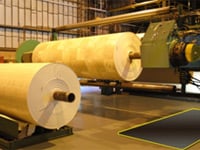
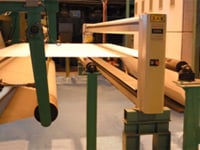
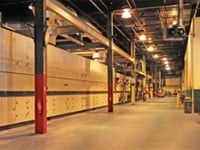
Vinyl resins, fillers and plasticizers are mixed into a thin paste that is spread on top of the printed image. This thickness of this wearlayer and recipe can change depending on the characteristics desired in the final product. The clear wearlayer is cured in a large oven. At the same time the previously applied gel wearlayer is expanded to three times its thickness to form the foam layer.
Texture is created in this stage as the inhibited ink does not expand. The wearlayer often contains natural materials or special additives that give the final product benefits such as antibacterial properties or easy clean properties.
This wearlayer is the surface of your flooring that you walk on.
The Back Coat Layer
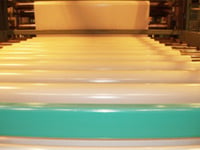
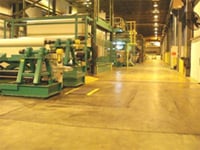
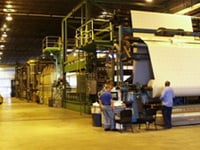
On Congoleum AirStep products a coating is also applied on the very back of the product. This back coat layer creates a product that can be installed without any adhesive and will stay flat on the floor. To create this layer we turn the product upside down and run the almost completed product thought the first gel process. The vinyl resins, fillers and plasticizers are once again mixed into a paste that is now spread onto the back of the product and then cured in an oven. The process is extremely slow and laborious because of the thickness of the coating and the time needed to cure it in the oven, but it creates an outstanding product that is exclusive to Congoleum.
Finished Product
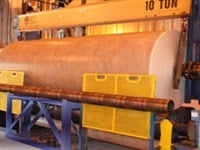
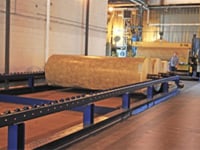
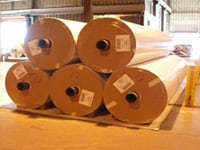
The final product is rerolled back into massive rolls that are then delivered to the Congoleum warehouse for distribution or storage.